the Characteristics of Condensation-Cure Mold Silicone
In the dynamic world of mold-making, the choice of silicone plays a pivotal role in determining the quality, precision, and versatility of the final product. Condensation-cure mold silicone, a distinctive variant in the silicone family, offers a range of features that make it a preferred choice for many applications. Let's delve into the unique characteristics that set condensation-cure mold silicone apart.
1. Precise Mixing and Curing Process: Condensation-cure mold silicone is a two-part composition, comprising silicone and curing agent. The optimal mixing ratio is 100 parts silicone to 2 parts curing agent by weight. The ease of operation allows for efficient blending, with a recommended working time of 30 minutes. Following the mixing process, the silicone undergoes a curing period of 2 hours, and the mold is ready for demolding after 8 hours. Importantly, the curing process takes place at room temperature, and heating is not recommended.
2. Semi-Transparent and Milky White Variants: Condensation-cure mold silicone is available in two specifications – semi-transparent and milky white. The semi-transparent silicone yields molds with a smoother finish, while the milky white variant exhibits resistance to temperatures exceeding 100 degrees Celsius. This versatility allows for the selection of the silicone variant that best suits the requirements of the intended application.
3. Range of Hardness Options: The hardness of condensation-cure mold silicone is offered in a spectrum ranging from 10A to 55A. The 40A/45A variant, recognized by its milky white color, is a high-hardness silicone, while the 50A/55A variant is specially designed for molding low-melting-point metals like tin. This diverse hardness range caters to various molding needs, providing flexibility and precision.
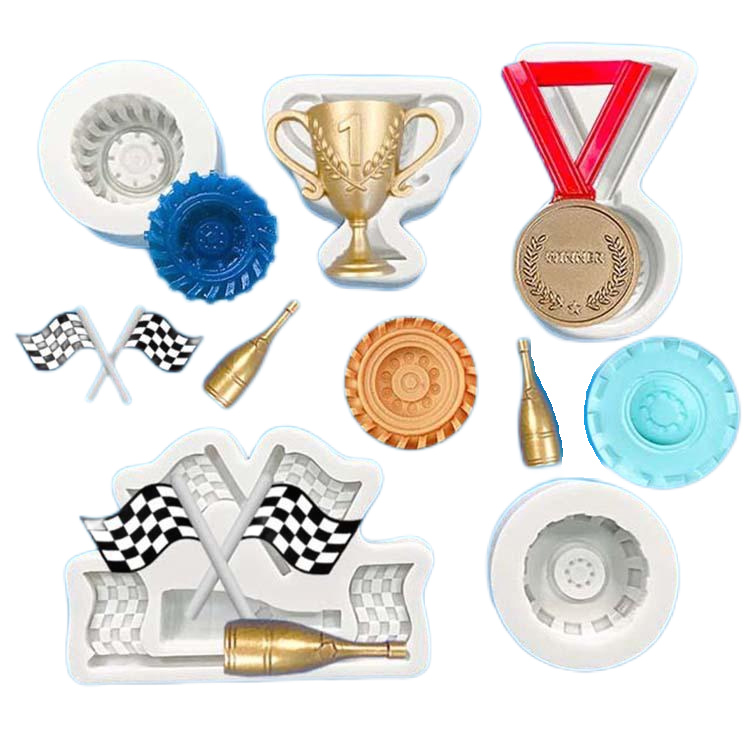
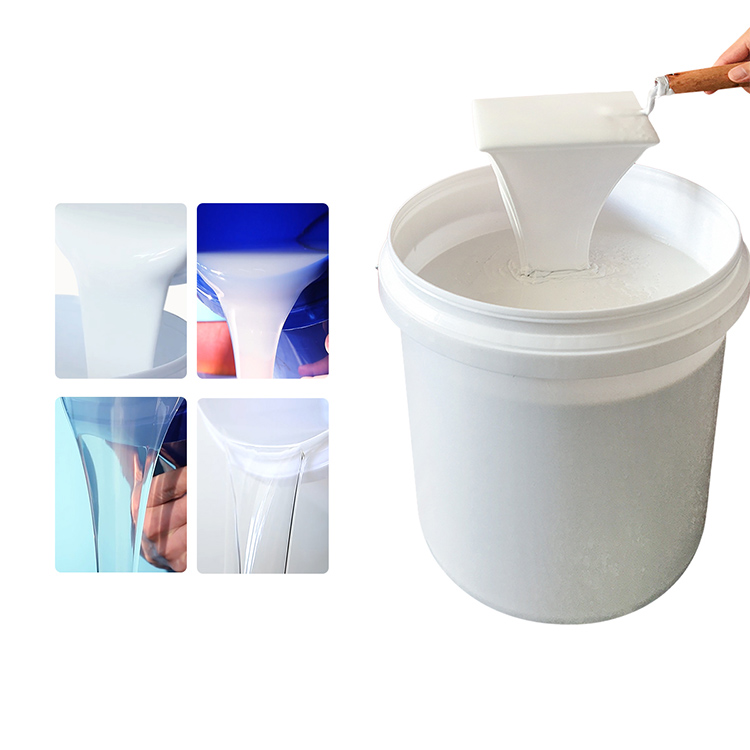
4. Adjustable Viscosity: Condensation-cure mold silicone exhibits a room temperature viscosity ranging from 20,000 to 30,000. Generally, as the hardness increases, so does the viscosity. The ability to customize viscosity ensures that the silicone can be tailored to meet specific requirements, offering a solution for a wide array of molding applications.
5. Organic Tin Cure and Catalysis: Also known as organic tin-cured silicone, the condensation-cure mold silicone undergoes a sulfurization reaction catalyzed by an organic tin catalyst during the curing process. The curing agent's proportion typically ranges from 2% to 3%. This organic tin cure mechanism contributes to the stability and reliability of the curing process.
6. Transparent or Milky White Liquid Form: Condensation-cure mold silicone is typically a transparent or milky white liquid. The versatility of this silicone extends to color customization, where pigments can be added to create molds in various colors, adding an aesthetic dimension to the final product.
7. Non-Toxic and Versatile Applications: Noteworthy is the low toxicity of condensation-cure mold silicone, making it a safe choice for users. The molds produced using this silicone can be employed in the production of a wide range of products, including gypsum, paraffin, epoxy resin, unsaturated resin, polyurethane AB resin, cement, and concrete.
In conclusion, condensation-cure mold silicone stands out in the realm of mold-making due to its precise mixing and curing process, hardness options, viscosity adjustability, organic tin cure mechanism, and versatility in applications. As a transparent or milky white liquid, this silicone provides a canvas for customization, allowing for the creation of molds that meet specific aesthetic and functional requirements. With its non-toxic nature, ease of use, and compatibility with various materials, condensation-cure mold silicone continues to be a trusted choice for craftsmen and manufacturers in diverse industries.
Post time: Jan-19-2024